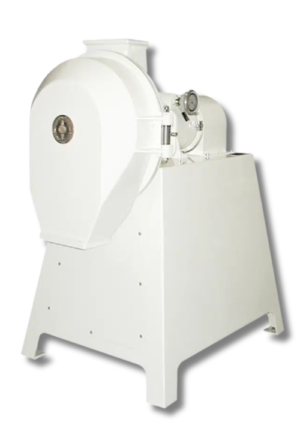
grinding mills
Discmill MHA 600
The Discmill MHA 600 is a highly versatile milling machine, widely used in Engsko milling plants for various grain milling applications. This powerful machine can efficiently break open cereal grains like wheat, or apply high-force grinding to reduce granular products into fine flour or wholemeal flour.
Designed for size reduction applications, the Discmill MHA 600 is an essential mill in the cereal grain milling industry, bridging the gap between roller mills and hammer mills. It provides a cost-effective solution for both grain processing and flour production.
Engsko adapt each Discmill MHA 600 to suit specific needs, selecting the optimal corrugation type, corrugation disposition (such as sharp-to-sharp or dull-to-dull), mill speed, and motor size for each application. This ensures peak performance and precision in the milling process.
One of the standout features of the Discmill MHA 600 is its easy-to-adjust grinding discs, which can be precisely calibrated using a micrometer handwheel. When the corrugated elements (tiles) become worn or require a different corrugation profile, they can be replaced in just one hour by a single operator, minimizing downtime and improving operational efficiency.
Whether you’re looking to process cereal grains or produce high-quality flour, the Discmill MHA 600 offers a reliable, customizable, and efficient milling solution, making it an indispensable part of milling plants worldwide
Technical data
- Motor power: kW 37
- Capacity kg/h: 1.500 - 2.000
- Dimensions: 1.335 x 890 x 1.530/70 cm.
why discmill mha 600?
The key feature of this unique grinding technology is its exceptionally high productivity relative to the machine’s physical size and energy consumption, making it an efficient solution for grain milling and flour production.
Highlight features
- Compact, self-contained design. Minimizes space requirement and installation cost
- Easily accessible and durable wearing parts. Keep maintenance costs low
- Rapid disc and element replacement. Minimizes downtime and operating costs
- Exchangeable grinding elements in various corrugation patterns. Covers a wide range of applications
- Simple, accurate handwheel adjustment of the grinding gap. This leads to consistent & uniform finished product characteristics
- Large grinding surface and no integral screen. Give high capacity and low power consumption